How To Get Stuck Wheel Spacers Off
Mathew was able to effigy out how to remove a stuck lug nut. He writes almost his tips and tricks.
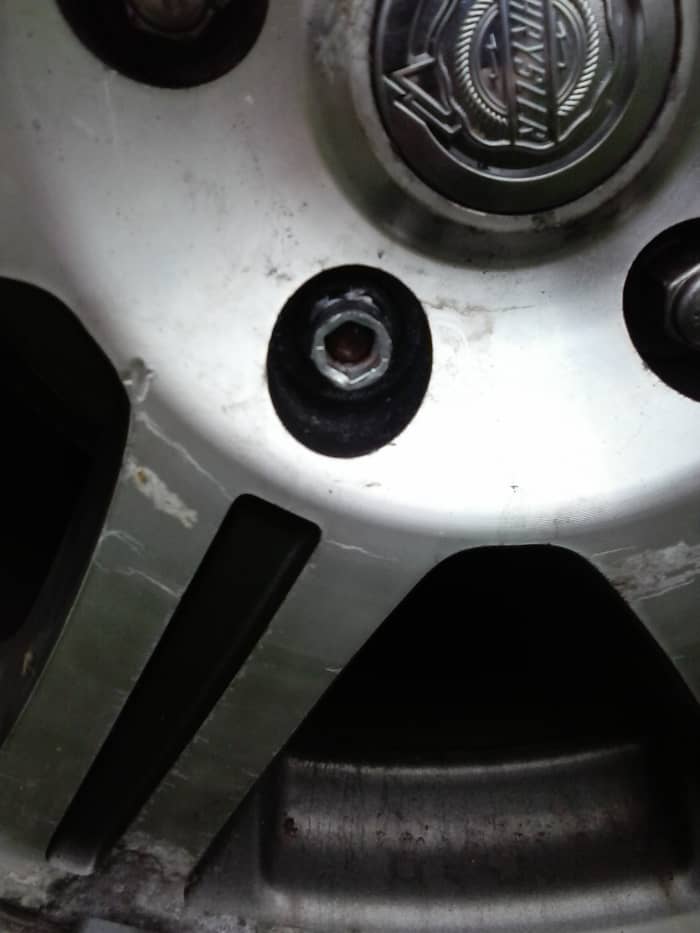
Stuck lug nut
How to Get a Stripped Lug Nut Off
A rather bad experience at a nationally known automotive tire store inspired me to write this article. I took my 2007 Chrysler Pacifica into the shop for a tire rotation. Commonly I do this maintenance myself, but I had a coupon for a free tire rotation, and so I thought I could salve some time and take it to the shop.
The front wheels came off without a problem. The rear passenger side wheel had a stuck lug nut. The mechanic was unable to remove it with his standard 6-point sockets and impact wrench. After he struggled for several minutes, he chosen me over and showed me a chewed-up-looking lug nut. He then proceeded to tell me that at that place was no style he could go it off and that I would have to have it elsewhere to get it removed. I was quite surprised. This was an auto shop defended to servicing tires. I would think that this problem would be encountered and dealt with regularly.
These results were completely unacceptable. I've dealt with this situation before, and at that place are very systematic ways of dealing with information technology.
- First off, I'll share which tools are needed to get the rounded lug nut off.
- Second, I'll review the mechanics of torque and force, so we tin can better understand the problem at manus.
- Third, I'll go through a stride-past-step guide that outlines the twist socket method.
- Lastly, I'll go over some preventative maintenance guidelines and brand sure you empathize what the proper torque is for your auto so you lot can avert the issue of over-tightening.
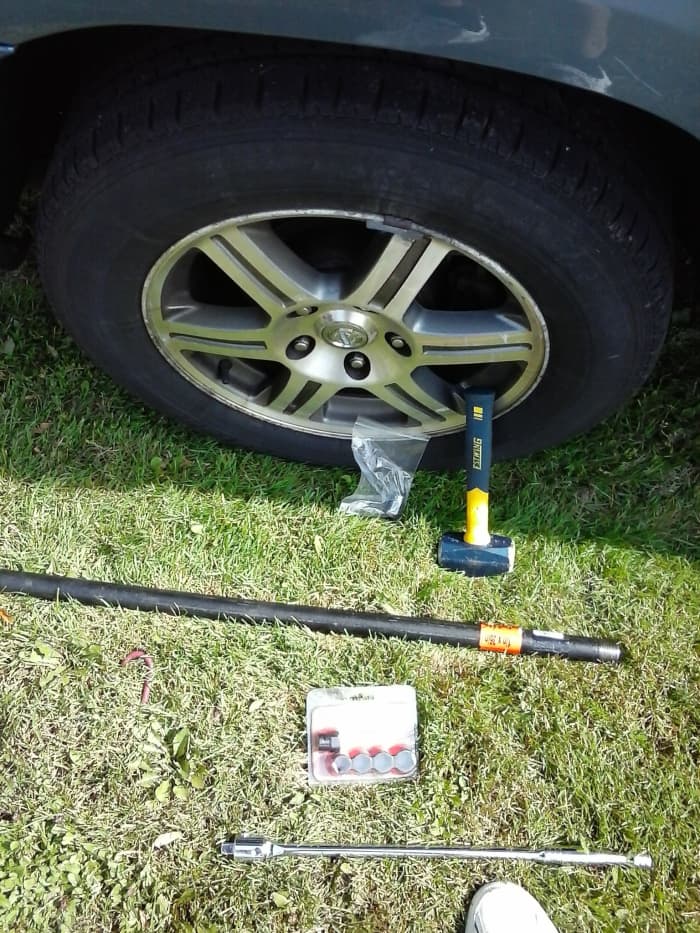
3 lb. hammer, 1/ii" drive breaker bar, 1/ii" bulldoze with hex caput nut extractor sockets, i"x36" iron pipe, and new lug nut.
- ½" drive billow bar $xv-20
- 1" diameter iron piping, 36" length $10-15
- Nut/bolt extractor twist socket set up $20-100
- 3 lb. hammer $v-10
- WD-forty or alternative penetrating oil $5
- Replacement lug nut $3
- Total cost: $58-153 (if you have to purchase everything)
Along with your other emergency supplies that are stored in your motorcar, I highly recommend keeping these items in the motorcar equally well, in case yous need to repair your own tires while abroad from home.
The Mechanical Advantage of Leverage
The physics of leverage can be summed up every bit torque. In the context of removing a lug nut from a wheel, we tin can call back of it as a simple statics problem.
- Torque = r x F
- Torque = rotational force at the lug nut
- X = Cantankerous production
- r = length of the breaker bar / leverage pipe
- F = Strength applied
I'd like to show how much torque you can generate with your body weight and compare it to the torque produced by a pneumatic impact wrench.
Impact wrenches used in auto shops range from 0-grand+(ft-lbs). Typically, between 0-400 ft-lb is more common.
Using a 24" breaker bar and a 36" fe pipe I'll bear witness you how much forcefulness your body weight alone can produce. Assuming y'all weigh 180lb here is the calculation of torque:
- Torque = r X ΣF [EQ 1]
- Torque = [(24in*(1ft/12in))+(36in*(1ft/12in))] 10 (180lb @ 90° vertical)
- Torque = 900ft-lb with 36" iron pipe and 24" breaker bar;
- Torque = 360ft-lb with 24" billow bar only
Of course, additional force can exist generated past jumping on the end of the pipe attached to the breaker bar. I'll show the calculation I used to discover how much torque is created from a half dozen" vertical jump on the cease of the pipe. To keep this adding as elementary as possible, I'll consider a stopping distance equal to the thickness of the sole of a sneaker combined with the estimated deflection in the lever (three"), and no free energy losses to the environment.
Gyre to Proceed
Read More than from AxleAddict
During this jumping activeness, we tin can say that at the peak pinnacle of your jump the initial potential free energy combined with the initial kinetic energy is equal to the sum of the kinetic energy and potential free energy when you are well-nigh to land on the end of the pipe.
- PE1 + KE1 = PE2 + KEtwo [EQ 2]
- PE = g*g*h [EQ 3]
- KE = 1/2*m*v2 [EQ 4]
- PE1 = Potential energy at acme of the jump
- KE1 = Kinetic energy at the peak of the jump = 0; no motion at peak of the jump
- PE2 = Potential energy right before landing = 0; the piping height = 0, that you are almost to state on
- KEtwo = Kinetic energy at the stop of the jump.
We can say that PE1 = KEii from the conservation of energy principle. We volition neglect the free energy losses due to friction, and elevate. Using this data we tin manipulate the equation to find how fast you are falling right earlier you land on the pipe (vtwo).
- (thousand*g*h)1 = (ane/ii*k*v2)2
- v2 = (2*g*h)1/2 [EQ 5]
- m = mass
- k = gravity
- h = height of jump (veritcal)
- v = velocity (vertical direction)
Considering the stopping distance (d) of 3", which is the thickness of your shoe and estimated deflection of the pipe. We can generate another equation from a piece of work-free energy principle. The change in kinetic free energy across the distance of the thickness of your shoe during the impact is divers as piece of work.
- Due west = ΔKE(impact) where KE at the end of the jump is 0
- Westward = 1/2*k*(vtwo)2 [EQ six]
Of form, nosotros know that Work is simply strength applied over a (bear on) distance:
- W = F2*d [EQ 7]
Putting [EQ half-dozen] and [EQ 7] together we tin detect F2 which is the (boilerplate) strength of touch.
- Fii = i/2*grand*(five2)2*1/d [EQ 8]
Combining this impact force from the jump with the forcefulness of your weight in the torque equation [EQ one], we take the following:
- Torque = r X [Strength of touch on]
- Torque = r 10 [([2*g*h]1/two)ii*i/2*m*ane/d))
- Torque = [24in*1ft/12in+36in*1ft/12in] X [[two*32.17ft/s2*0.5ft]*1/2*(180lb*1slug/32.17lb)*(1/0.25ft)]..................<slug is just lb*s2/ft>
- Torque = 2160ft-lbs when you lot jump on the end of the breaker bar and pipage extension
And a quick recap of what we looked at:
- Torque = 900ft-lb with 36" iron pipage and 24" breaker bar
- Torque = 760ft-lbs if you jump on the 24" breaker bar only
- Torque = 360ft-lb with 24" breaker bar simply
- Bear upon wrench = 0 - 1000ft-lbs
Nosotros encounter that an iron pipe with a breaker bar will be plenty enough strength to overcome over-tightening.
Step i: Breaking Upwardly the Rust
Utilise targeted, liberal amounts of WD-40 to the base of the lug to allow this penetrating oil to be drawn into the commodities threads through capillary action. If it is desperately rusted, then give information technology a few smacks with a hammer to break some of the rust-free before applying the penetrating oil. Give the penetrating oil fourth dimension to work, up to a 24-hour interval if you lot take the time.
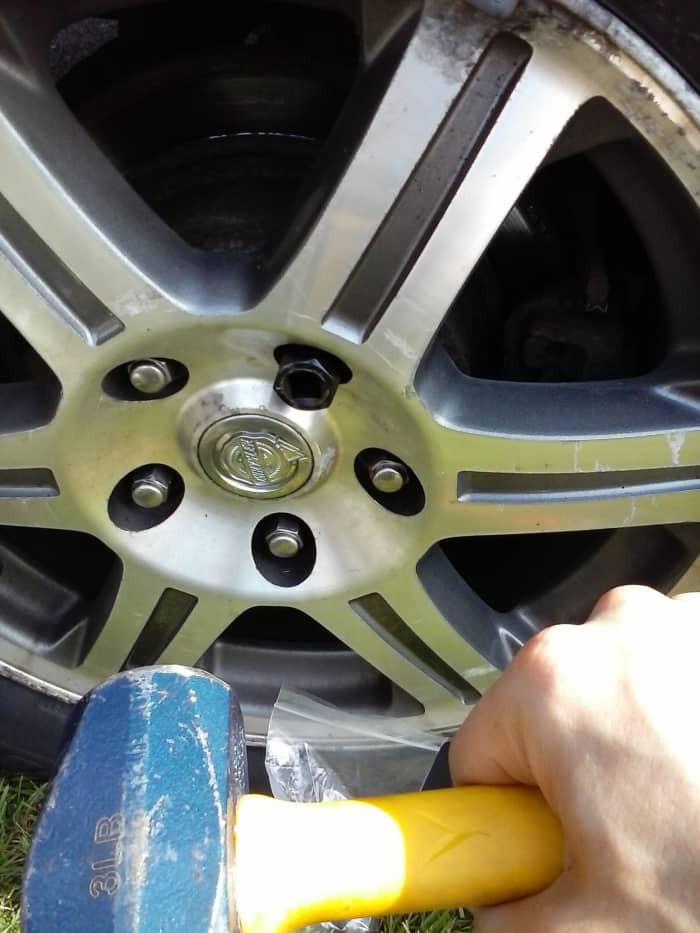
Socket needs to be hammered downward very tight otherwise it will sideslip off.
Step 2: Selecting the Correct Nut Extractor Socket
The nut extractor socket needs to be a tight fit onto the lug nut. So tight that you must hammer it down tight with a 3 lb. hammer. These specialty twist sockets are really bully; once seated properly, y'all can turn the socket and it will grip the nut tighter.
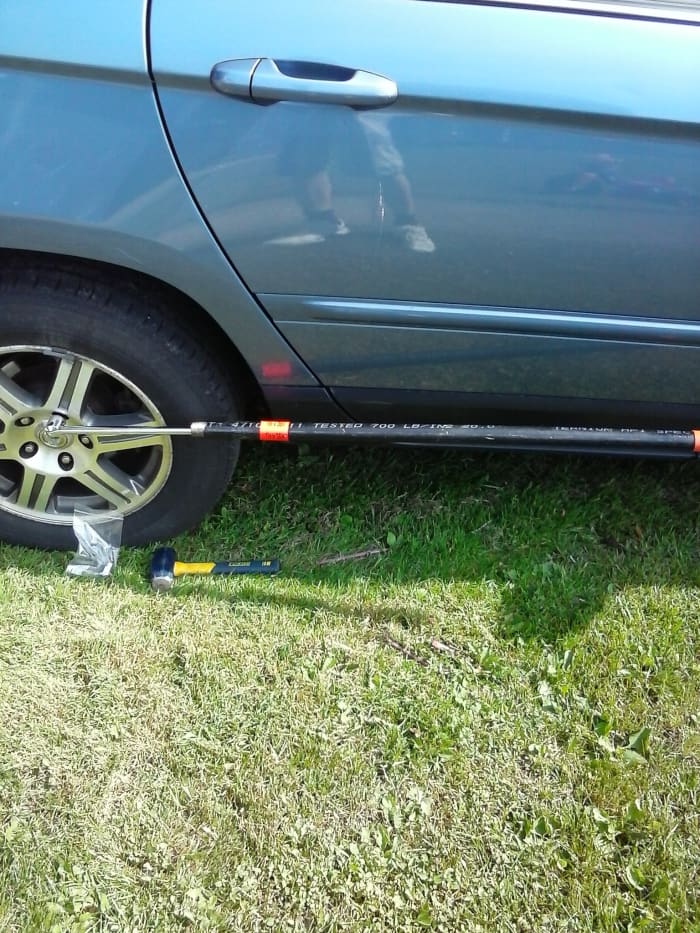
Breaker bar and iron pipe total of 5' length will give me around 900 ft-lbs of torque
Step 3: Getting the Lug Nut Off
Adhere the ½" drive billow bar to the nut extractor socket. If y'all need to, slide the 36" iron pipage over the breaker bar handle to gain an additional mechanical advantage. If the right extractor socket was used (no slippage), and so this force will costless the lug nut. Definitely throw it out and supersede with a new one.
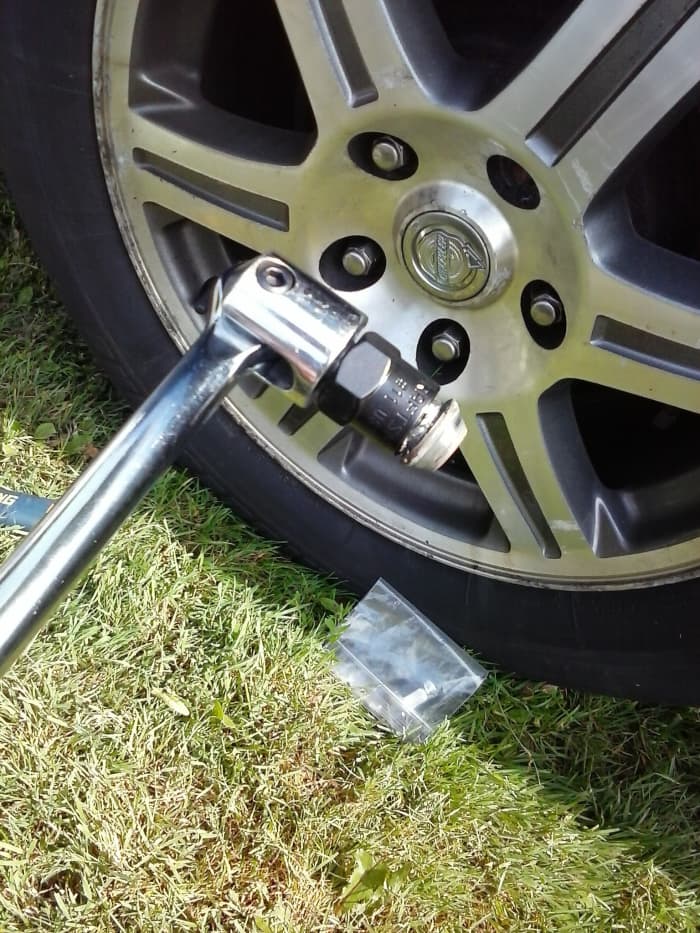
Lug nut is off with the socket.
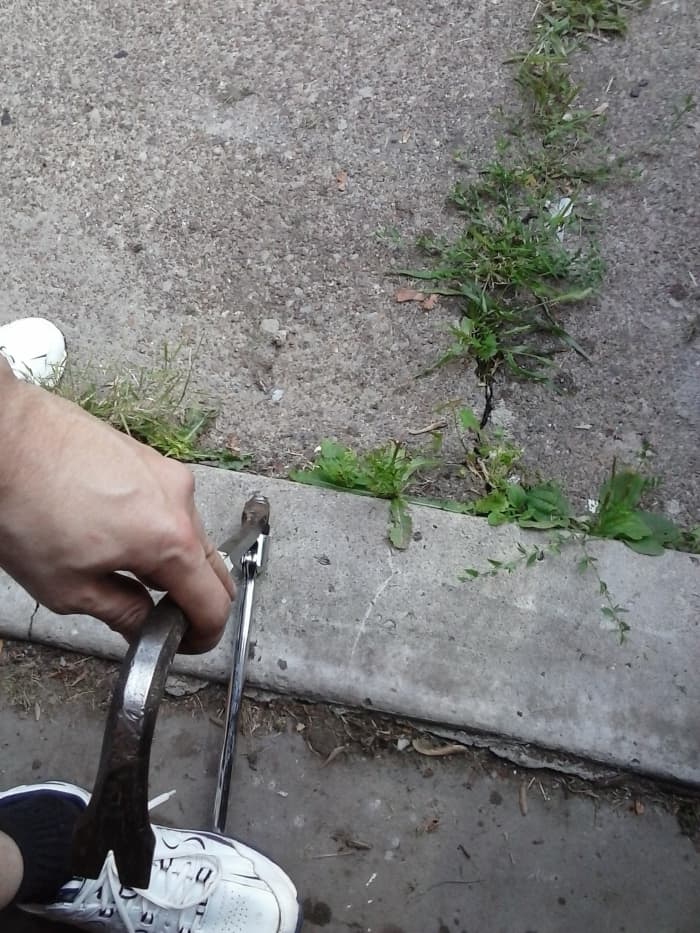
Either punch it out in a vice or hammer the crowbar as shown.
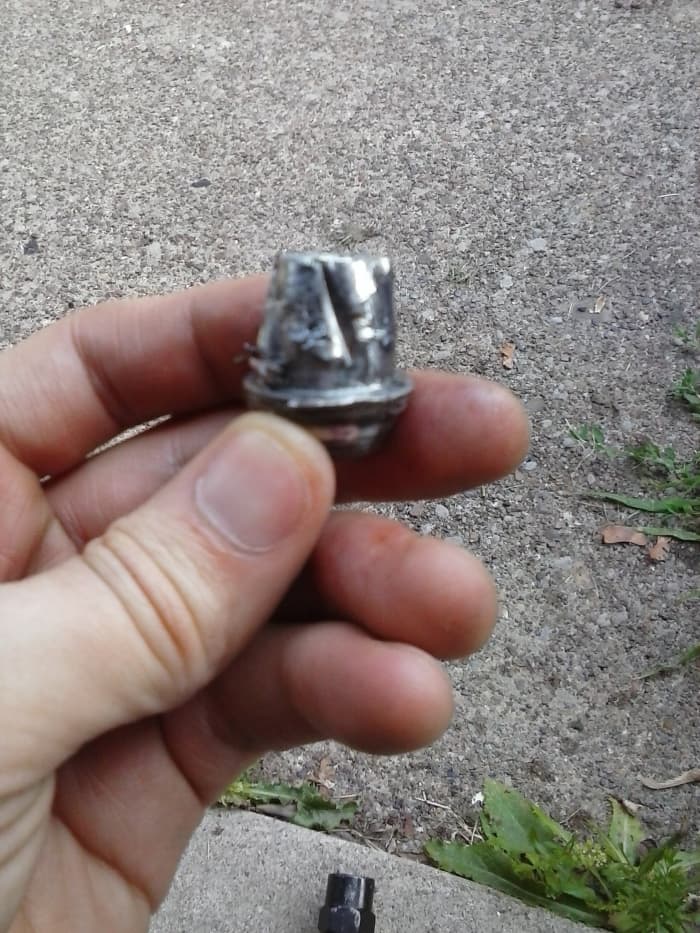
Close upwardly view of what the lug nut looks like afterward. Note the grooves made by the twist socket.
Alternative Strategies
While this method usually works, at that place are bug that tin be encountered that will crave different strategies.
- If the stud is stripped: The lug spins freely merely won't come off the stud. Drill through the lug and/or stud. Select a carbide drill bit that matches the size of your stud. Use heavy pressure level while drilling at low speed to drill down the middle of the lug until it is no longer attached to the stud. There are some specialty drill $.25 available on the market that I haven't tried. The videos look promising, and then if you lot experience like taking a chance, and spending extra money I've included a link to one of these products. Annotation: Drilling through the stud will require you to replace it, which can be rather catchy for some vehicles.
- Can't grip the lug nut with twist sockets: If you take access to welding equipment, and so tack weld a nut to the damaged 1 so y'all tin have a clean grip again. Or, split the lug with a chisel. Use a heavy 2-4 lb. hammer for this and make sure you accept a sharpened chisel. Split the lug nut down the side. Conscientious not to impairment the rim. Audit stud for damage, it may need to exist replaced.
Preventing the Problem
Careless mechanics can easily overtighten the lug nuts with their impact wrenches. Consider speaking with your mechanic to make sure the right torque will be applied before they start working on your machine. Bear in mind that different cars take different requirements for torquing lugs. Cars typically require threescore-100ft-lbs of torque. Larger vehicles tin can require upwards of 300ft-lbs of torque. Consult your owner'due south manual for correct torque requirements.
Keep lugs clean and free of water. Dirt, h2o, and rust on the threads and mounting bolts must be removed before attempting to put your wheel dorsum on.
If they are worn out and don't seem to fit very well, there is nothing incorrect with getting a new ready.
This commodity is accurate and truthful to the best of the author's cognition. Content is for informational or entertainment purposes only and does non substitute for personal counsel or professional advice in business concern, financial, legal, or technical matters.
How To Get Stuck Wheel Spacers Off,
Source: https://axleaddict.com/auto-repair/How-to-remove-a-stuck-or-stripped-lug-nut-from-your-car-or-truck
Posted by: scottoted1938.blogspot.com
0 Response to "How To Get Stuck Wheel Spacers Off"
Post a Comment